A critical requirement for many unmanned air vehicles is the improved fuel economy. Recuperators can reduce fuel consumption and expand the mission endurance for gas turbine-powered UAVs. The recuperator heats the compressed air before combustion thereby reducing the amount of fuel need to heat the exhaust stream and spin the power turbine. Frontline Aerospace has developed an additive manufacturable recuperator design that creates very large heat transfer coefficients using microturbulators within each layers of the compact heat exchanger. This results in very small cores with low pressure losses. Frontline projects have proved our approach and we have fabricated full-size recuperators for the Rolls-Royce Model 250 gas turbine and validated thermal performance. The use of additive manufacturing has been key to producing strong, rectangular and non-rectangular compact heat exchanger cores. Creating headers to carry the compressed air in and out of the heat exchanger can also be complicated and additive manufacturing is very helpful. Use of both aluminum and titanium in recuperator system designs can further decrease weight and increase recuperator performance. All these Frontline Aerospace innovations further contribute to the range, endurance and time on station for turbine powered UAVs.
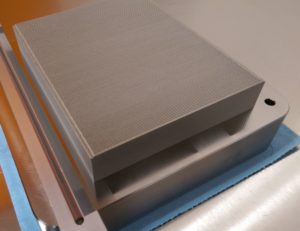
Frontline’s MicroFire™ recuperator is a special-purpose high temperature cross-flow heat exchanger that extracts heat from the hot engine exhaust and transfers it to the compressed engine air before combustion. Depending on specific implementation, this can improve the overall thermal efficiency of the engine by as much as 100%.
The historical challenge with recuperators in aircraft applications centers on the need for low-weight, low-volume materials and designs that can withstand the pressure and thermal shock, while assuring heat-transfer efficiency. The graph below shows the tremendous improvement in thermal efficiency that is possible with recuperators.
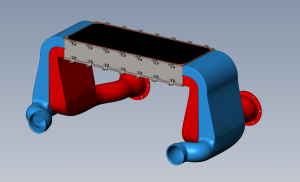
The patented MicroFire™ recuperator solves these challenges for aircraft. It improves specific fuel consumption by as much as 40% with very low pressure drop and power loss (less than 3%), all for under 50 pounds of recuperator weight for the Rolls-Royce C20 engine series.
This is a key enabling technology to dramatically increase helicopter engine endurance and reduce Specific Fuel Consumption (SFC), while also reducing hydrocarbon emissions.
Microfire™ Part Close up of micro-channels
MicroFire™ Recuperator Summary:
- Drop-In Retrofit for Gas Turbine Engines
- Quick Payback and ROI
- ~40% Fuel Savings
- Improved Range And Endurance
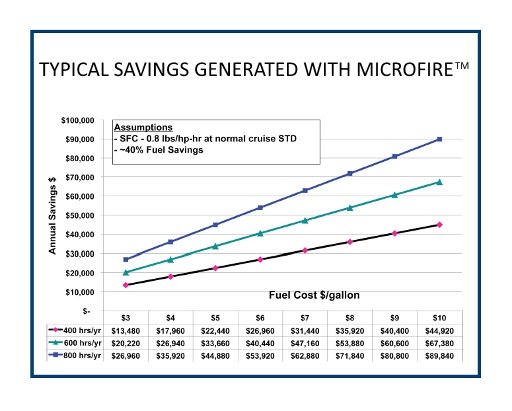
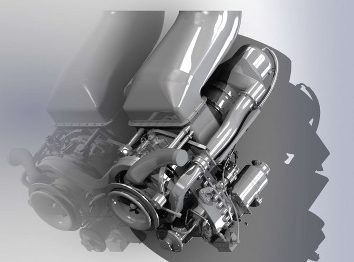
In Cooperation With StandardAero – A DAE Company
- Facilitate MicroFire recuperator testing and refinement
- Collect engineering data for FAA supplemental type certificate submission
- Ensure good value propositions for helicopter owners and operators
- Promote energy conservation and pollution reduction aspects of MicroFire Recuperators
Related Video
Related Downloads
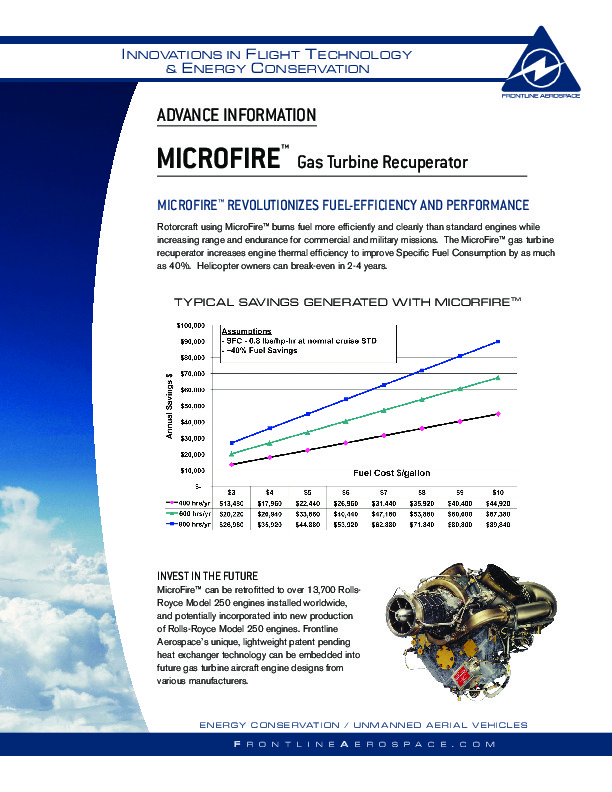
MicroFire™ Datasheet 2.76 MB 37 downloads
Abstract: Rotorcraft using MicroFire™ burns fuel more efficiently and cleanly than...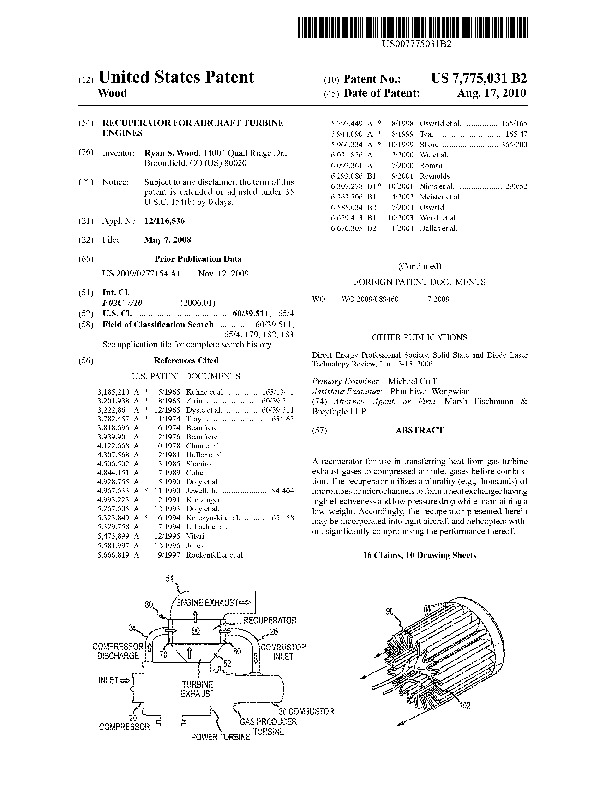