New Compressor Technology Boosts Power and Thermal Efficiency for Gas Turbines
Gas turbines need to compress air for combustion. Over the decades much work has been done to optimize the efficiency of airfoils, stator rows (stationary airfoils) and compressor blades (spinning) to improve the efficiency of this compression process, which is typically about 80%. At each stage of compression the air increases in temperature and pressure and demands more power and energy to compress it. Frontline’s IsoCool™ product reduces the amount of power and energy required to compress the air by removing heat from each axial stage of compression via our patent-pending Q-Blade™ Technology. Depending on the pressure ratio, turbine power and application, this can save 5-10% in fuel and increase available horsepower by 10-15%.
Frontline’s initial focus is on Rotorcraft using the Rolls-Royce Model 250 C20 and C20R series as well as ground-based 501K turbines (now made by Siemens) used for utility electric or industrial mechanical power. A simple retrofit replaces the existing compressor housing with new Q-Blade™ stator rings and a liquid cooled housing. Heat extracted during the air compression cycle is dumped via a radiator to the atmosphere. This retrofit significantly improves the thermal efficiency of the gas turbine.
Video of IsoCool™ in Production:
Related Downloads
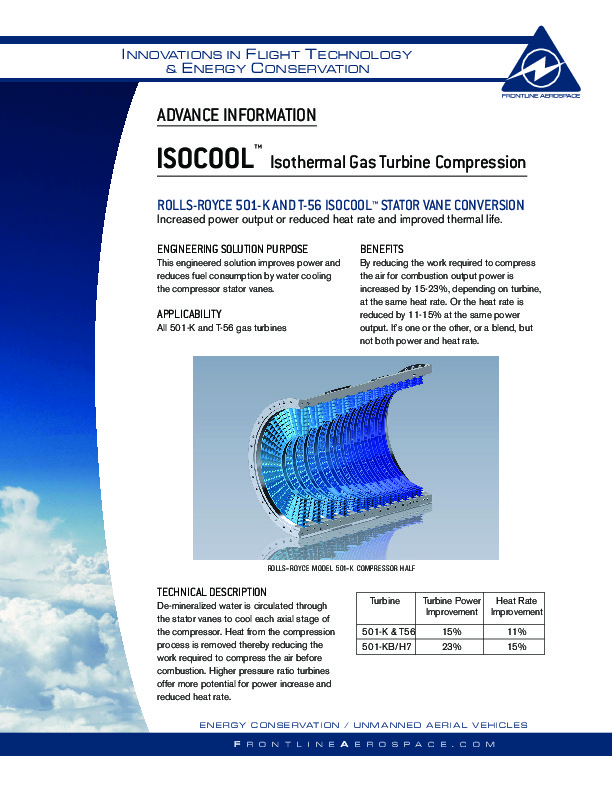
IsoCool 501K / T56 Datasheet 535.56 KB 13 downloads
Abstract: Rolls-Royce 501-K and T-56 Isocool™ Stator Vane conversion kit. Increased...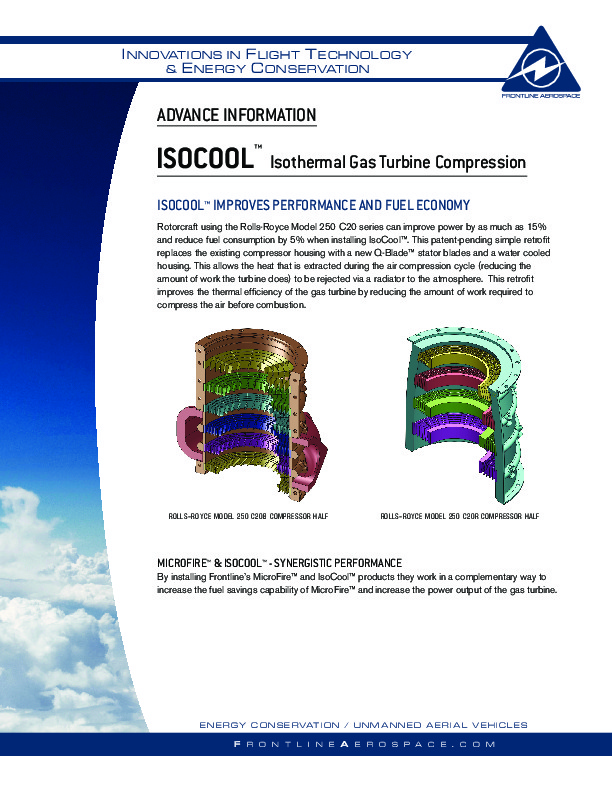
IsoCool Datasheet 1.41 MB 18 downloads
Abstract: Rotorcraft using the Rolls-Royce Model 250 C20 series can improve power...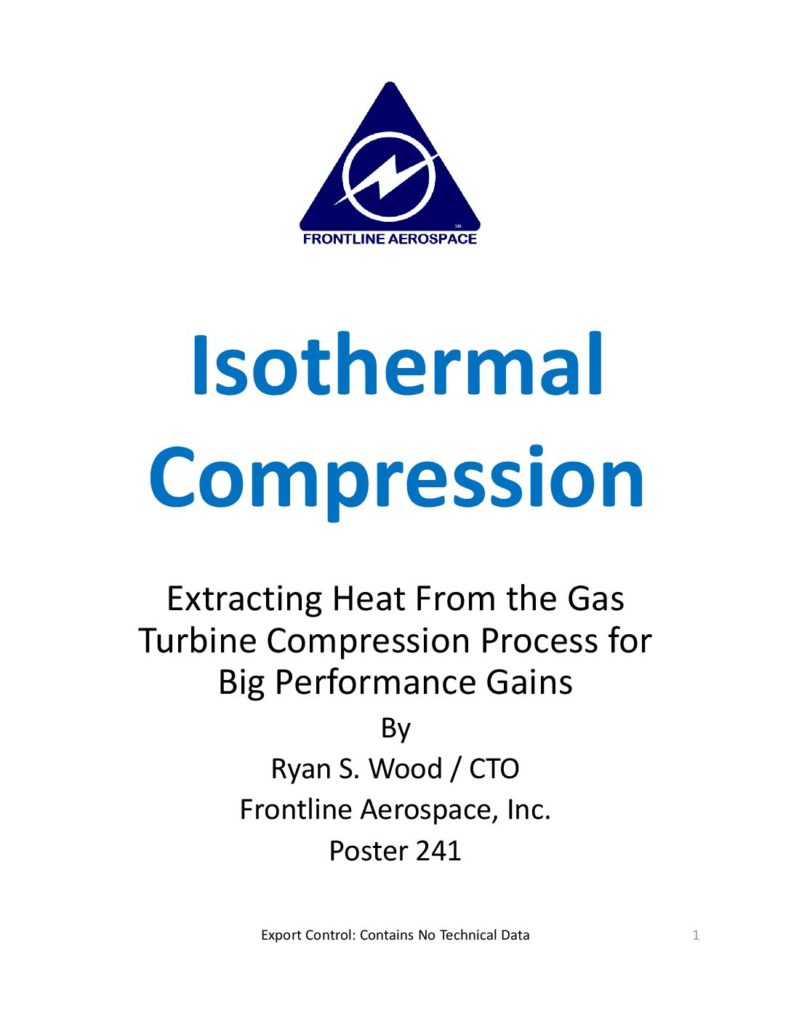
IsoCool Defense Innovation Summit Poster 1.12 MB 10 downloads
Abstract: Gas turbines need to compress air for combustion. Over the decades much...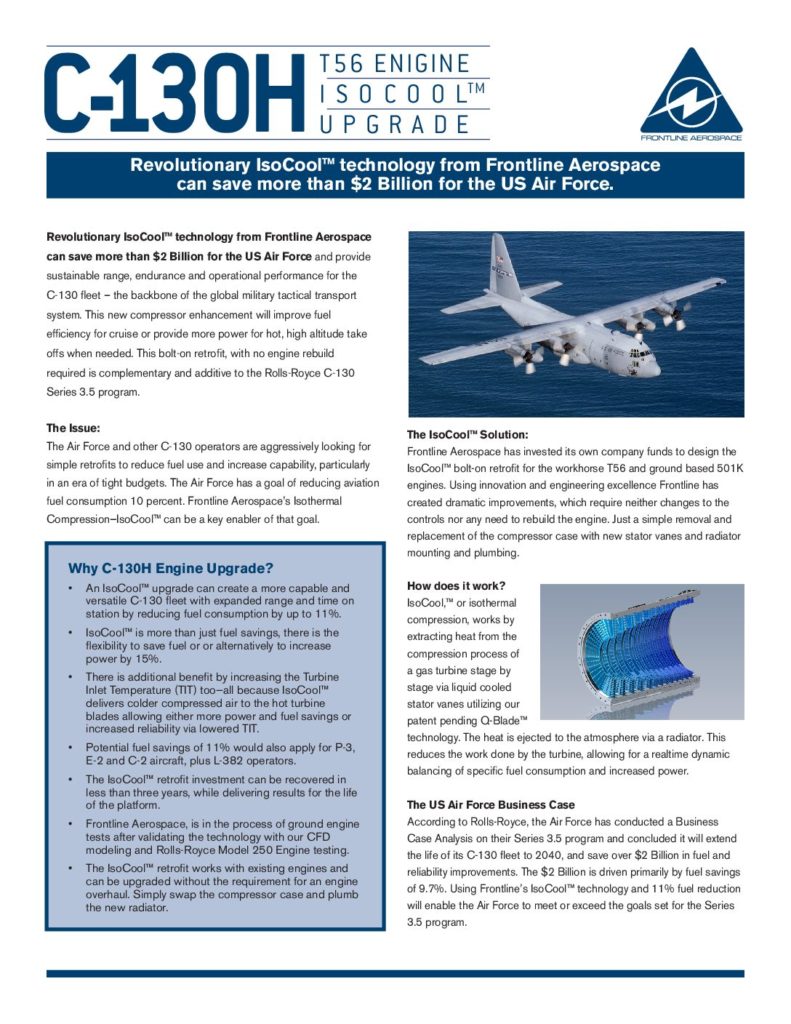
IsoCool for C130H 825.82 KB 10 downloads
Abstract: Revolutionary IsoCool™ technology from Frontline Aerospace can save more...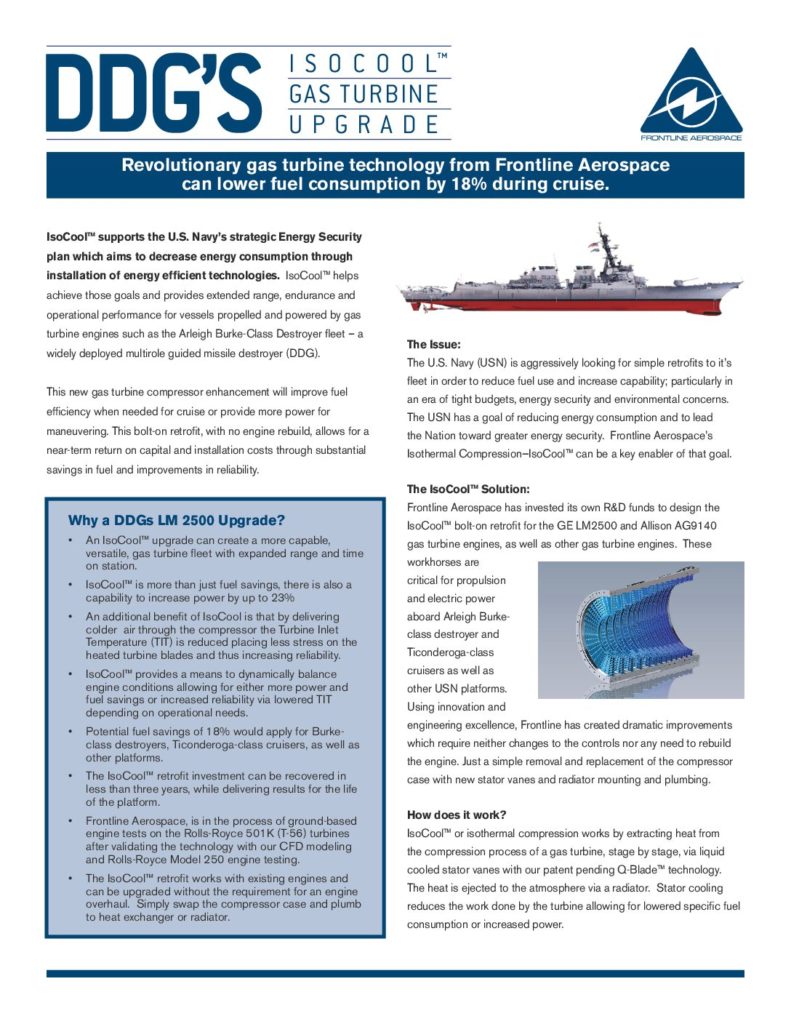