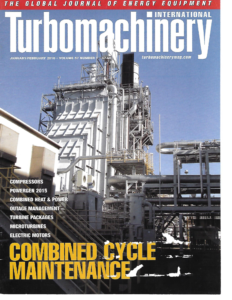
ISOCOOL: ADVANCED BRAYTON CYCLE TURBINE MODIFICATIONS CAN BOOST POWER, LOWER HEAT RATE AND EMISSIONS
According to thermodynamic principles, when the temperature of gases entering a turbine exceeds the temperature of gases entering the compressor, the turbine can deliver more power than the compressor consumes. Therefore the engine can produce a net power output.
The efficiency with which the engine converts heat energy into mechanical energy depends on many factors. Such as the compressor and turbine efficiencies, temperature levels, pressure ratio, and the presence or absence of enhancements, such as regeneration and compressor air-stream cooling. The power produced is proportional to the efficiency as well as the mass flow rates of air and fuel.
Conventional gas turbines operate approximately according to the ideal gas turbine or Brayton cycle. This cycle embodies reversible adiabatic (without heat transfer) compression of atmospheric air, addition of heat at constant pressure, reversible adiabatic expansion through a turbine back to atmospheric pressure, and exhausting to the atmosphere.
Regeneration greatly improves fuel economy by recovering much of the exhaust heat. When regeneration is employed, the cycle is designated a regenerated Brayton Cycle.
In a non-regenerated engine, lowering the compressor-discharge temperature causes an increase in the fuel flow rate needed to maintain the turbine inlet temperature at its set value. However, the incremental increase in the required combustion heat is matched by an incremental increase in the net power output.
Then efficiency, being net-power divided by combustion-heat-rate, also increases with compressor cooling. When regeneration is coupled with compressor cooling, efficiency increases even more…
Download and Read the Full Article: